How Supply Chain Delays Are Affecting the Pointe Shoe Industry
If I had a dollar for every time I heard the phrase “global supply-chain delays” in the news, I’d be able to purchase a year’s supply of pointe shoes. But in reality, these international delays have had a big impact on pointe shoe manufacturers, too, causing a backup that might leave an empty shelf where your size and style are meant to be. Amy Taylor, the director of production for Kansas City Ballet who also manages shoe orders, says, “I’ve had to go to one of [my dancers] and say, ‘Hey, you don’t have any shoes in stock. Do you need another bottle of Jet Glue?’”
The delays are part of the pandemic’s ripple effect, with the recent Omicron surge heightening the uncertainty. Read on to learn how the industry is coping, and how to prepare for a possible dearth in your own pointe shoe stockpile.
Breaking Down the Pointe Shoe Supply Chain
Pointe shoes start off as a collection of raw materials, like satin, paste, cardstock, cotton and, for companies like Gaynor Minden, elastomerics. Brands either source these materials from outside suppliers or make them in-house at their factories. A high amount of logistics and planning goes into these early stages. For example, Christine Wilson, CEO of Virtisse, says that satin sourcing is critical. “You want to ensure that your satin is consistent and there are no dye-lot differences. You don’t want to have to change that manufacturer or supplier.”
The factory is a key nexus, where cobblers or machines assemble the shoes before they are shipped in bulk to distribution centers. Virtisse’s typical pallet, or unit shipment, from its factories weighs 1,500 kilograms (that’s over 3,000 pounds of pointe shoes) and goes to the company’s warehouse outside Philadelphia. The shoes are then packaged into smaller shipments to fulfill orders from ballet companies and retailers. From there, of course, they end up on dancers’ feet.
From Pandemic Quiet to Sudden Demand
As dance organizations started ramping back up again last fall, supply issues arose. Miriam Jurgensen, Ballet Austin II’s head of wardrobe, notes that in July and August, as companies and schools reopened and prepared to start their seasons, they ordered an influx of pointe shoes. When it came time for dancers and shoe room managers to restock for Nutcracker in October, Jurgensen says, many still faced delays from early-season orders. It was a snowball effect, leaving some scrambling for solutions to make it through the holiday ballet run.
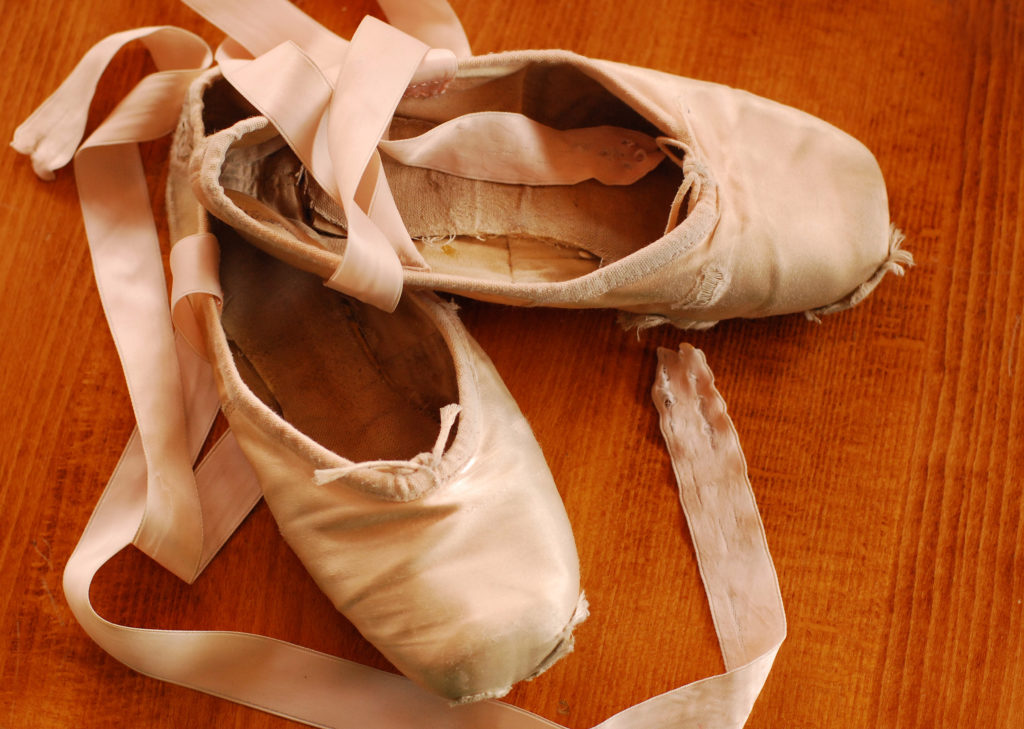
Taylor orders each female Kansas City Ballet member 65 pairs of shoes per season; she actually had a surplus after company shutdowns in 2020. Entering into the 2021–22 season, however, she noticed delivery issues. “There was probably about a five-month delay between what the estimated time was versus when we actually had them.” Fortunately, about 80 percent of her company members have special-order shoes, which are ordered months in advance. She notes that younger KCB dancers and apprentices—those more likely to use a stock shoe (and who may not have had any overstock with the company to begin with)—were more greatly affected.
Factory Shutdowns and Shipping Delays
Meanwhile, supply is still trying to ramp up to meet demand’s return to normalcy. “Before the pandemic, we were able to receive shipments from our factories about every two weeks,” says Kristen Klein, special orders manager for Freed USA. But ongoing COVID concerns often have factories operating at reduced capacity, spacing out labor shifts to protect employees or shutting down entirely in the face of outbreaks. Virtisse has factories located in South China and Moscow. “Omicron has recently shown up in China,” says Wilson, “which has a zero-tolerance policy for COVID.” She adds that inflation, as well as the sanctions and humanitarian crisis resulting from the Russian invasion of Ukraine, will undoubtedly exacerbate an already challenging situation.
Perhaps the greatest effect has been on shipping timelines. “Airlines are running fewer flights,” says Klein. Sick workers from the Omicron surge this year meant there were fewer pilots and staff members at airports. She says it’s tougher to get a spot on an airplane, and she’s seen shipments get stuck in customs for inordinate amounts of time.
The monthslong delays are one consequence; higher prices are another. “What may have been $5 a kilo is now an additional $6 a kilo to ship,” says Wilson, more than doubling her shipping costs. She has decided not to pass this cost through to her customers, with the hopes that the stressors on shipping will soon ease. Gilbert Russell, of Brio Bodywear in Ottawa, Canada, confirms that other brands have had to adapt: “Some prices that have been stable for quite some time have jumped quite a bit. For example, some $90 shoes have gone to $105.”
Creative Solutions
Not everyone down the supply chain has been equally affected. Larger ballet companies seem to have fewer problems than the small to midsize organizations. “I’m sure larger companies have larger overstocks,” says Jurgensen. Jurgensen and Taylor are both part of a digital community of company shoe-room managers who are buying overstock shoes amongst each other to get their dancers what they need.
Diversifying your supply sources is good advice for individual dancers, as well. If your preferred shoe is out of stock at your regular dancewear store, you may need to search further afield, or ask your local retailer if they can work with you to find a new fit.
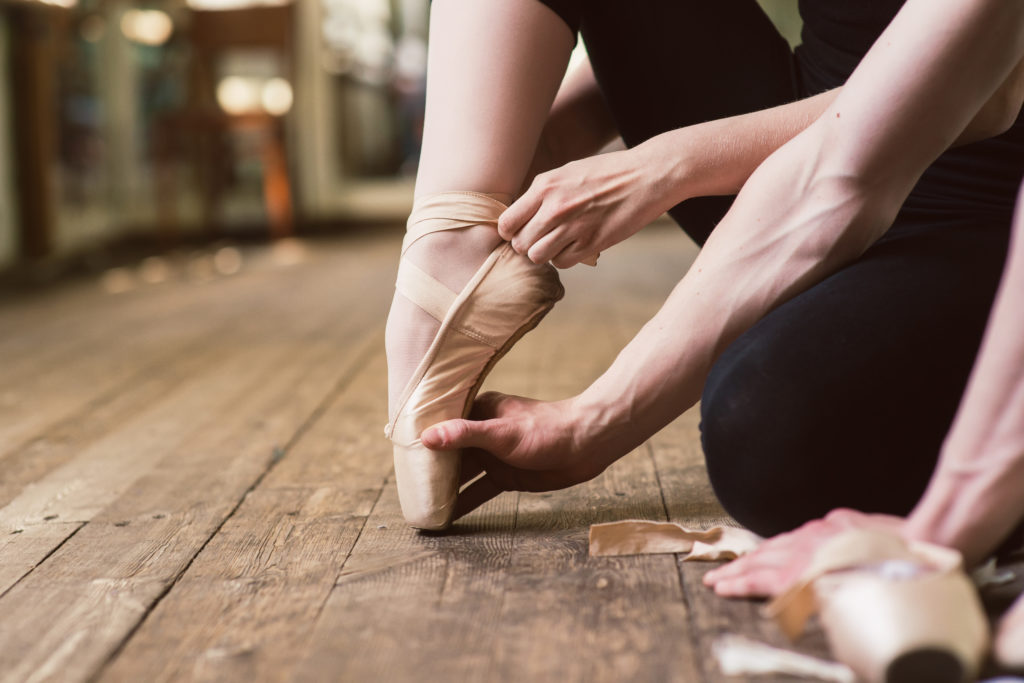
Russell stocks nearly 40 models. In the instances where a customer’s shoe is out of stock, he tasks himself and his fitters to get creative. He doesn’t love the adage that you can go shorter and wider. “If you poured water into the shoe, I’m sure it would come out the same volume, but your foot’s not like that,” he says. Instead he thinks it’s better to keep your correct length and go up a width. He suggests certain padding tricks to help with fit, like an adhesive insole insert to make a longer shoe a little snugger and to lower the profile on your foot.
Embrace Contingency Plans
Planning ahead and stocking up extra shoes whenever you can is evergreen advice that all of our experts recommend. Klein and Wilson are both opting for transparent communication with their customers, believing that being honest about ongoing delays will help companies, retailers and dancers better prepare for the rest of the year. In early 2022, neither brand believes everything will snap back to normal.
Anything from pandemics to natural disasters to global politics to your preferred shoemaker retiring may affect your supply. For dancers, a shake-up might even be a blessing in disguise. Klein says that the pandemic downtime gave dancers the chance to address slight imperfections they were noticing in their fit. “Some even found that their feet changed over the pandemic,” says Klein. An open mind and experimentation might give you a better shoe than you had before.